Hypercare: Prepare your People
The goal of this hypercare series is to provide as much practical information as possible. Too many articles share nebulous insights without clear direction or takeaways. The goal is to build out a toolbox for any software implementation. With experience in SAP, Oracle, Manhattan, Fishbowl, Excalibur and many others, our concepts can be taken into virtually any hypercare scenario.
In, “Hypercare: Prepare for the Worst to Deliver the Best”, we discussed a few considerations for successful post-go-live support. We focused on preparing for disruption in an uncertain landscape including discussions related to: Covid-19, staff shortages, remote tools, and how to react when losing key SMEs during or after implementation. In this article, we will continue to discuss tangible ways to put your employees in the best position for go-live success.
Systems and People
A successful hypercare is correlated to thorough process design, solution design, solution testing, implementation execution, and change management phases. Hypercare is the period used to address problems that were not identified in those phases. If your solution is not technically sound, your chance of successful implementation is zero, no matter how well your hypercare is planned. Still, in my experience, the solution design usually works well enough to keep a facility operational. Change requests and adjustments to the solution can be expedited with extra development staff present for hypercare. There will always be technical challenges and ways to improve after implementation that were not encountered in testing. Could the process have been better? Could the system have added functionality? Was some component missed during testing? Of course, but system issues are rarely “showstoppers”. Systems are predictable; they execute instructions and code. On the other hand, employees are far from predictable. We will use a case study approach to illustrate what is most often the most unpredictable and largest inhibitor to successful implementation, your people.
Introduction to TruckCo
Warehouse workers and staff at TruckCo notice multiple visitors from corporate walking around their facility taking notes and having hush conversations. C-suite executives wander the aisles in heels and polished oxfords. Rumors swirl that something new is about to happen, but no one knows exactly what.
A few months later, TruckCo’s corporate office released an announcement. TruckCo will introduce new ERP system functionality into all warehouse/distribution centers in the network. It is estimated that over $900,000 per year is lost due to inventory shortages. After analysis it is determined that TruckCo inventory shortages are tied to untimely put away of materials, not availability of products in the warehouse. The new functionality will increase efficiency in receiving/put away times that allow for more products to be shown as “in stock” for order builders/pickers.
A team was assembled of FTEs and consultants to train all warehouse receiving personnel within the TruckCo network. Office staff in the receiving office were taught to manually receive items and reconcile inventory in the new system. Warehouse teams were also trained in how to properly receive and put away items. The TruckCo training team felt good, knowing all training went well and without any major issues or red flags.
TruckCo-Go-Live/Hypercare
One month after go-live, most warehouses in the TruckCo network were still struggling with receiving errors in the new system. The TruckCo corporate office was beginning to wonder whether the new receiving technology was still a good idea. Warehouses reported little to no system downtime. The technology seemed to work, but efficiency numbers were much lower than before the new system implementation. Warehouse personnel seemed to be at a loss. Morale and system buy in was at an all-time low.
Recommendations
TruckCo is a fictional representation of a common outcome in any system go-live. There could be a myriad of reasons for TruckCo go-live challenges, but in this case, system functionality was not the issue. The system was predictable and functioned as designed. Warehouse personnel were not prepared. There are several ways to create more consistent and predictable results from your people.
1. Understand the differences in current (pre-implementation) warehouse processes across the network.
Where are processes in different facilities justifiably different and where should they be made the same before go-live. Address and set process expectations well before go-live?
2. Understand current (pre-implementation) system workarounds that are not officially part of a process but are commonly used by employees.
Articulate the importance of not using workarounds in a new process understanding old habits die hard. Understand how these workaround habits could have a negative effect on the new system/process. Make your people more predictable by understanding why the workarounds exist and for what problems they were created to solve.
3. Always map old to new processes.
Ask warehouse personnel to record their normal workday. What do they do when they first come in? What is the typical order in which they execute tasks? Write out daily tasks, including processes both inside and outside of IT systems. Be sure to include all reports that must be pulled. Understand which reports may not be available or may look different in the new system. Create a document that compares pre/post go-live processes. Overlay process and places personnel should input system data very explicitly.
Example: In the old system I created a sales order in SAP transaction VA01. In the new system sales orders will be created by the sales team through a batch job. I will need to look up sales orders in SAP transaction VA03 then proceed with the next step.
Lay the comparison of process out in a grid. Lay the process out from start to end of shift. Hint: Tell personnel to use this process-to-process sheet after go-live as a “cheat sheet”.
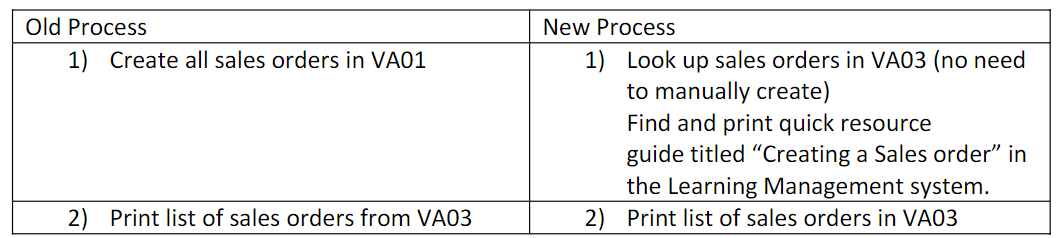
4. Understand the preparedness of each shift.
Day shift teams tend to be more predictable. They usually have better coverage and expertise. Ensure all shifts are adequately trained. Build a go-live schedule that sets your facility up for success and distributes your best personnel as evenly as possible across all shift changes. Understand who wasn’t trained due to preplanned paid time off, sickness, or other factors.
Lack of preparation creates unnecessary stress for all employees. Stressed employees are more likely to quit or make rushed decisions that can have a colossal effect on a go-live. Warehouses communicate on a regular basis. When a facility is about to make a system change that another facility just completed, all facilities rarely go-live at the same time, the first thing that happens is a phone call. “I heard you guys went live with the new ERP system…. How was it?”. Perception of go-live success or failure impacts every other facility’s mood, buy-in, and success in the future implementations. Prepare your people so you can be prepared too.